BAUSCH+STRÖBEL - Liquid Filling Line - ESM 10010
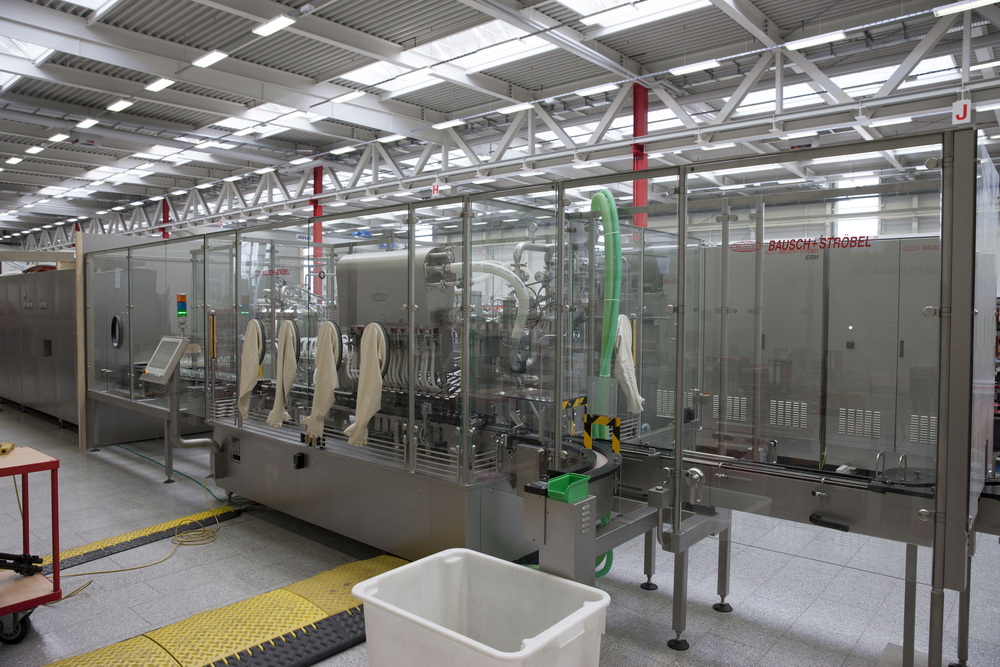
Specifications
Manufacturer | BAUSCH+STRÖBEL |
Model | ESM 10010 |
Year | 2015 |
Condition | Used |
Serial Number | MLTC-D-B020 |
Stock Number | MLTC-0001-WH |
Description
BOTTLE WASHING/STERILIZING/FILLING/CLOSING LINE BAUSCH & STRÖBEL
Year of construction: 2015
System for filling infusion bottles for lipid emulsions and closing with rubber stopper and aluminium cap.
The entire plant from 2015, but never put into operation. Originally factory-packed and complete in wooden crates.
- Parts in contact with product made of stainless steel AISI 316L
- Connection 230/400V/50Hz
- Output max. 5,800 bottles/h, with sterilisation in DHT 62125 and CFDA-conditions 4,000 bottles/h (100 ml), 2,250/h (250 ml), 1,500/h (500ml)
- Usable bottle sizes (depending on formats): diam. 16-98 mm, height 85-180 mm
- Available formats for glass bottles: 100, 250 and 500 ml
- Usable rubber stoppers (depending on formats): diam. 12-35 mm, height 6-18 mm
- Usable crimp caps (according to formats): diam. 12-40 mm, height 6-18 mm
- PLC Siemens S7
- HMI Bausch & Ströbel OVD (Operation, Visualisation, Data collection and Evaluation) basic operating 15 inch touch panel PC
- Operating system Windows Embedded Standard 7
- Menu languages D, E, CH
- User administration according to 21 CFR part 11 EU GMP Annex 11
- Ethernet interface
- Compact Flash Card (CF)
- UPS for HMI
System consisting of:
Washing machine AWU 6030 (ultrasonic)
- Max. temperature 85°C
- 8 stations
- Bottle feeder in bulk
- Pre-cleaning by ultrasonic device
- Main cleaning by ultrasonic device
- Recirculation
- 3 different cleaning liquids can be used
- PLC Siemens S7-300, servo motors Jetter with Jetter Control
Sterilising tunnel DHT 62125
- 1 preheating zone with prefilter F5 according to DIN EN779
- 5 sterilising zones slightly turbulent LF with filters class H14 and H13 according to DIN EN1822
- 2 cooling zones length 2,700 mm with pre-filter F5 according to DIN EN779 and slightly turbulent LF with filters class H14 according to DIN EN1822
- Monitoring for airflow with Photohelic differential pressure gauges
- Monitoring for filters with Magnehelic differential pressure gauges
- Monitoring for temperature with PT 100
- 12-channel recorder
- PLC Siemens S7-300, AC/DC motors
Filling/gassing/evacuation/plugging machine ESM 10010 (CIP/SIP)
- Dosing tank 100L, pressurised
- 10-position intermittent bottle transport in line
- 2 sorting pots for cap feed with 2x5 stopper feed rails
- Gas flushing during filling
- Time/pressure filling system (low shear forces)
- Electronically adjustable needle movements for overhead filling
- Evacuation before capping with rubber stoppers, alternatively with or without gas exchange
- CIP/SIP system (Cleaning in Place / Sterilising in Place) for the entire dosing system incl. 100L dosing tank
- PLC Siemens S7-400, servo motors Jetter with Jetter Control
Closing machine for aluminium caps (crimp caps) RVB 4080
- Cap hopper
- Sorting bowl
- 8 stations capping unit in rotary cycle
- PLC Siemens S7-300, AC/DC motors